This technical bulletin presents useful guidelines for selecting the appropriate personal protective equipment (PPE) for working with methylene diphenyl diisocyanate (PMDI)(1) and PMDI-based foam systems, and analyzes the performance characteristics of several gloves, coveralls, splash suits, and other protective suits commonly used when working with PMDI.
Health and Safety Concerns
During the handling, processing, and application of PMDI, contact with PMDI in vapor, liquid, or particulate form may cause a range of adverse health effects, including irritation and sensitization to PMDI. Short or long-term exposure to PMDI can affect the skin, eyes, and respiratory system. Chronic dermal exposure can lead to skin irritation and/or skin sensitization, and may cause respiratory sensitization.
Engineering controls and sound workplace practices should be the first line of defense against PMDI exposures, and guidelines have been established to help individuals avoid overexposure and adverse health effects(2). Nevertheless, it is important that employees wear any personal protective equipment recommended for their specific job functions.
Eye and Respiratory Protection
In addition to the gloves and suits analyzed later in this bulletin, individuals working with MDI and PMDI containing products should consider the use of appropriate eye, face, and respiratory protection.
Eye Protection
In situations where there is splash potential, it is strongly recommended that employees wear goggles or safety glasses and, depending on the extent of potential contact, a faceshield. These situations include line-breaking (transfer hose disconnect), transfer of material using a drum pump, etc. Diisocyanates may irritate the eyes and can be difficult to remove, so prevention is very important.
Respiratory Protection
The use of air purifying (cartridge) respirators is now approved in certain situations as part of a comprehensive respiratory protection program(3). An organic vapor cartridge with a particulate filter may be used where the concentration of PMDI in air can be documented, and it is verified that the sorbent capacity will prevent breakthrough. A cartridge change out schedule must be part of the respiratory protection program. When concentrations of diisocyanates exceed the protection afforded by a cartridge respirator (e.g. emergency situations), an air-supplying respirator should be used.
Clothing Selection
Employees should understand and adhere to safe handling practices for PMDI and other chemicals that pose potential health hazards. This may include wearing eye protection, respiratory protection, gloves, and coveralls or lab aprons. For individuals who work with PMDI, appropriate protective clothing is essential for the prevention of skin exposures.
When selecting protective clothing, the following factors should be considered:
Chemical Resistance of Glove or Garment:
To be effective, the protective clothing should resist penetration by the chemical or chemicals being handled. Use of disposable gloves and clothing is often preferred, because proper decontamination of reusable items may be difficult. Protective gloves and garments should also be resistant to penetration by solvents used in combination with PMDI.
Specific Job Functions:
The nature of the job being performed will greatly influence the selection and features of protective clothing. For example, analyzing foam samples in a laboratory may require light-duty gloves (less than 10 mils in thickness) that are flexible and preserve manual dexterity; on the other hand, a maintenance project, such as repairing a pump line, may require thicker gloves that are rugged and durable. When the manual dexterity requirements of some jobs require the use of thin, form-fitting gloves that offer limited amounts of protection time, the use of such gloves is acceptable if the gloves are changed with sufficient frequency.
Potential for Exposure:
The degree of exposure risk for individual job functions will help determine the degree of personal protection required and the appropriate clothing for the job. For instance, work conducted in a laboratory environment, where the potential for exposure is limited, may only require gloves, eye protection, and a lab apron or lab coat. On the other hand, a project that presents a greater risk of acute exposure, such as loading and unloading tank cars, may require the use of hooded coveralls, boots, and more substantial gloves (heavy duty and light duty) to ensure adequate protection.
Duration of Exposure:
The length of time that an individual is working with or handling PMDI will influence the type of protective clothing selected. When working with PMDI for extended time periods, protective clothing that offers the greatest level of chemical resistance is recommended.
In addition to these factors, individual work habits, industrial hygiene practices, and personal experiences will influence decisions made when selecting protective clothing.
Research Approach
The International Isocyanate Institute (III) sponsored a study in which Texas Research Institute (TRI) evaluated materials from more than 50 items of chemical protective clothing—35 gloves of 10 different materials and 17 suits of 14 different materials—to determine the degree of resistance to permeation offered by each garment.
The III research measured the length of time it took PMDI to permeate through the protective clothing material under conditions of continuous contact and complete surface coverage with PMDI.
Following that survey, TRI was commissioned to conduct solvent and PMDI breakthrough testing on several different gloves and eight solvents, each containing one percent PMDI by weight.
Discussion of Tables
Tables 1 and 2 are organized by glove or garment type, and, within each category, are arranged in descending order according to the protection time provided(4). These tables also include the trade name, manufacturer, thickness, and durability of each item.
The PMDI protection times presented in Tables 1 and 2 are the times required for PMDI to penetrate the chemical protective glove or garment material, and are the maximum suggested use times. The wearer should understand that gloves and garments should be changed often enough to avoid exceeding the listed protection times and to prevent contact with PMDI. For example, if a job requires the use of thin, flexible gloves with a 30 minute protection time, then the wearer should change gloves within 30 minutes of initial contact with PMDI.
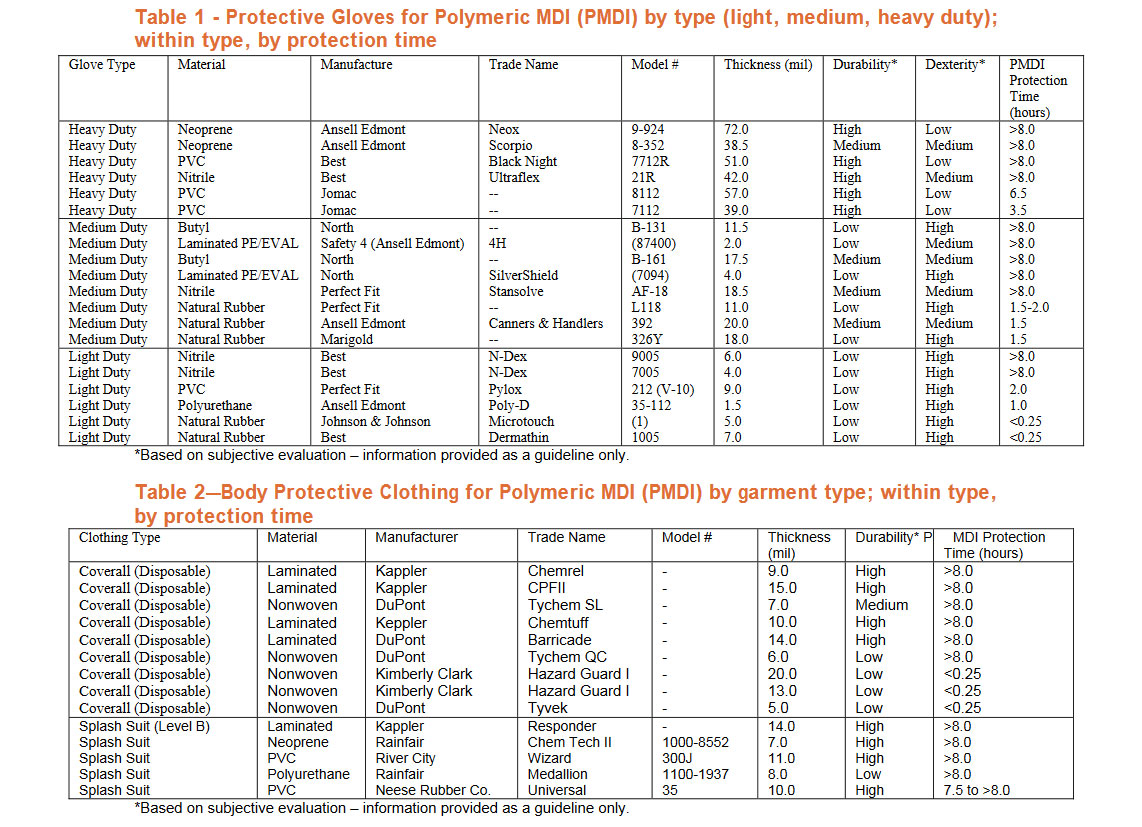
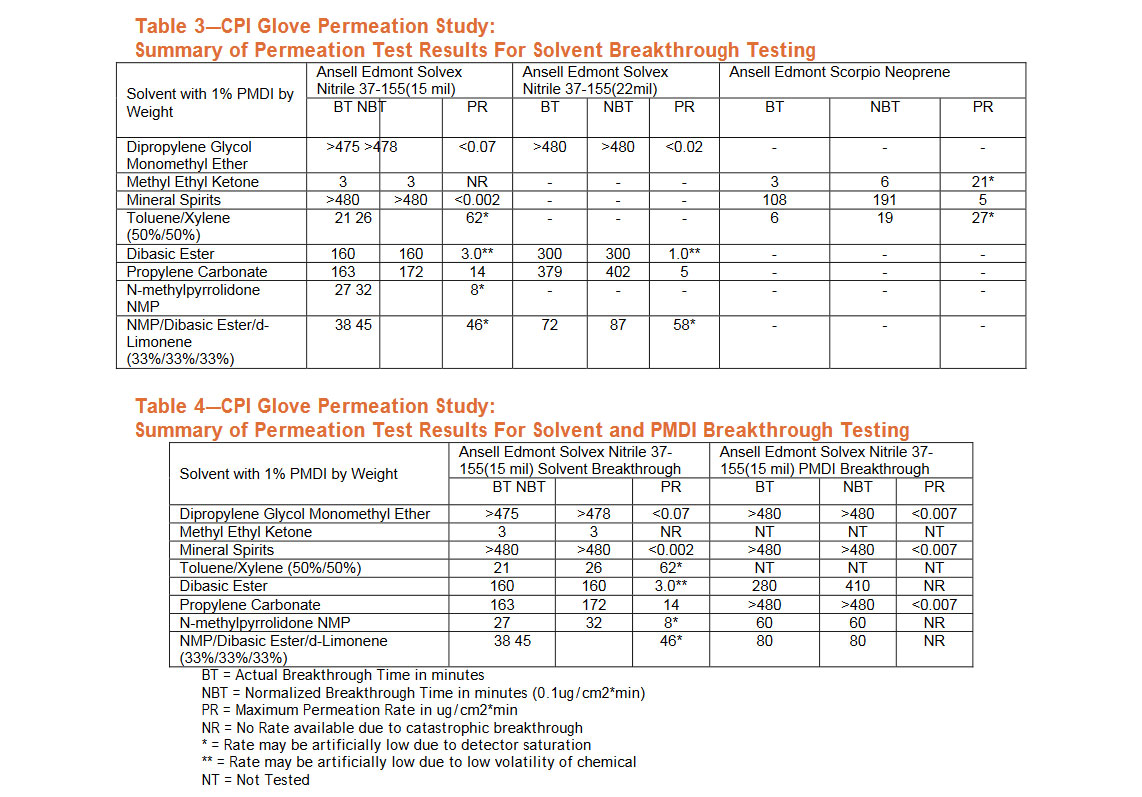
Tables 3 and 4 present various glove materials and the corresponding breakthrough times, in minutes, of several solvents and solvent-1% PMDI mixtures(5). It is important to assess not only the degree to which protective garments prevent PMDI penetration, but also the degree to which they prevent penetration by any solvents used.
Although a large number of chemical protective gloves and garments were tested, this technical bulletin is not intended to be a comprehensive review of every piece of protective clothing currently available. Other gloves and garments not included in this study may provide equivalent protection.
Individuals who work with PMDI should keep themselves informed of new protective clothing developments and consult their protective clothing suppliers and manufacturers.
Additional Information
For additional information on PMDI protective clothing, safe handling, and disposal, consult the following sources:
Guidelines for the Selection of Chemical Protective Clothing, American Conference of Governmental Industrial Hygienists 6500 Glenway Avenue, Building D-7, Cincinnati, Ohio 45211-4438
Technical Data Sheets (TDS) and current Material Safety Data Sheets (MSDS) for polymethylene polyphenyl isocyanates (PMDI) available from the supplier. Working With MDI and Polymeric MDI: What You Should Know (Technical Bulletin AX205), Alliance for the Polyurethane Industry 1300 Wilson Blvd., Suite 800, Arlington, VA 22209
Hyperreactivity and Other Health Effects of Diisocyanates: Guidelines for Medical Personnel (Technical Bulletin AX150), Alliance for the Polyurethanes Industry 1300 Wilson Blvd., Suite 800 Arlington, VA 22209
MDI-Based Polyurethane Foam Systems: Guidelines for Safe Handling and Disposal (Technical Bulletin AX119), Alliance for the Polyurethanes Industry 1300 Wilson Blvd., Suite 800, Arlington, VA 22209
Guidelines for the Responsible Disposal of Containers and Wastes from Polyurethane Raw Materials Processing (Technical Bulletin AX151), Alliance for the Polyurethanes Industry 1300 Wilson Blvd., Suite 800, Arlington, VA 22209
W. Robert, et al., Protecting Workers from PMDI Solvent Combinations—What Gloves Work Best? Proceedings of the Polyurethanes Conference 2000, Sponsored by the Alliance for the Polyurethanes Industry 1300 Wilson Blvd., Suite 800, Arlington, VA 22209
Model Respiratory Protection Program for Compliance With the Occupational Safety and Health Administration Respiratory Protection Standard 29 CFR §1910.134, Alliance for the Polyurethanes Industry 1300 Wilson Blvd., Suite 800, Arlington, VA 22209
(1) In the U.S., MDI is the usual abbreviation for “pure” (as opposed to modified or polymeric) diphenylmethane diisocyanate, or methylene diphenyl diisocyanate, or methylene bis (p-phenyl isocyanate) or diisocyanatediphenylmethane. However, certain manufacturers and end users also use “MDI” to refer to the undistilled mixture of 4,4’-diphenylmethane diisocyanate and higher molecular weight fractions. Other synonyms for MDI are isocyanic acid: p,p’methylene diphenyl ester; and 1,1’-methylene bis (isocyanato benzene). There also are “polymeric” forms of MDI, which typically consist of 30-70 percent diphenylmethane diisocyanate and the balance in higher molecular weight fractions. The CAS Number for polymeric MDI is 9016-87-9.
(2) For details, see API Technical Bulletin AX205, “Working With MDI and Polymeric MDI: What You Should Know,” API Technical Bulletin AX119, “MDI-Based Polyurethane Foam Systems: Guidelines for Safe Handling and Disposal,” and Technical Bulletin AX150, “Hyperreactivity and Other Health Effects of Diisocyanates: Guidelines for Medical Personnel”
(3) For more details on when air purifying respirators are allowed under the new OSHA Standard, please refer to API Model Respiratory Protection Program for Compliance With the Occupational Safety and Health Administration Respiratory Protection Standard 29 CFR §1910.134
(4) Protection times refer only to the time required for PMDI to penetrate the garment and do not address penetration by solvents or PMDI-solvent combinations.
(5) For details on the permeation of PMDI/solvent combinations see W. Robert, et al., “Protecting Workers from PMDI-Solvent Combinations—What Gloves Work Best?”
This document will be continuously updated on the API website: www.polyurethane.org This bulletin was prepared by the Alliance for the Polyurethanes Industry as a service to the polyurethanes industry. It is intended to provide some useful guidance for selection of protective clothing for workers handling methylene diphenyl diisocyanate (PMDI). The information herein is offered in good faith and is believed to be accurate and reliable as of the date of publication; however, it is offered WITHOUT WARRANTY, EXPRESS OR IMPLIED, AS TO MERCHANTABILITY, FITNESS FOR A PARTICULAR PURPOSE, OR ANY OTHER MATTER. Consult an attorney or other appropriate professional with specific questions relating to your specific operation.
©2001 The American Plastics Council doing business as The Alliance for the Polyurethanes Industry.