RESISTANCE CONTROL MODE |
Resistance Control Mode (RCM) allows full temperature control of your heated hose without depending on hose RTD cables and a FTS. If you are not using this free upgrade on your Reactor 2 machine here are a few reasons why you should. |
RCM is Graco's patent pending, heated hose temperature control technology. RCM allows you to have full temperature control of your Graco heated hoses without depending on the hose RTD cables and FTS for temperature monitoring and control. RCM can be used on all standard Reactor 2 machines with software 4.01.001 or newer installed. |
BENEFITS OF RCM |
- Less Downtime - Broken RTD cables and fluid temperature sensors are no longer an issue. No time needed to do repairs.
- Less Repair Costs - Buying parts to repair broken RTD cables and FTS sensors is eliminated. No labor costs required to perform these hose repairs.
- Improved Yield - Optimize your material yield with consistent and accurate hose temperature control. RCM provides more consistent heating, eliminating hot and cold spots of material within the hose. In addition, if your hose is running in "Amp Mode" or "Manual Hose Heat Mode" your material temperature is not being accurately controlled, therefore you are sacrificing material yield.
- Increased Productivity - Less down time due to troubleshooting hose alarms. Increased performance by spraying with a hose providing consistent and accurate temperature control.
- Free Upgrade - RCM works with your existing Graco heated hoses.
|
HOW TO USE RCM |
- Update your Reactor software to the latest version 4.01.001 or newer if your Reactor does not already have this software.
- Enter Setup Mode on the ADM and navigate to System Screen 3.
- Select "Resistance" from the drop down menu.
- Upon initial installation, follow calibration procedure.
|
RCM CALIBRATION |
- Calibration is the process by which a calibration factor is stored to the Reactor’s memory. In order to save a calibration factor, the Reactor will correlate the measured resistance at the time of calibration to the temperature at the time of calibration.
- The most important detail about obtaining an accurate calibration factor is the calibration should be done when the entire system (Reactor and hoses) are at the same ambient condition. The optimal time is first thing in the morning before the primary heaters or hose heat has been turned on.
- Once the hose’s resistance is saved to a known temperature, the system will then measure changes in the hose’s resistance. The hose resistance will change as temperature changes, and the system will be able to calculate temperature by monitoring changes in resistance.
- Calibration is only required at time of initial set-up, and will take only a few seconds to perform. Recalibrating would only be required if: – a section of hose has been replaced – a section of hose has been added – a section of hose has been removed – over time, hose temperature does not seem to be controlling accurately.
|
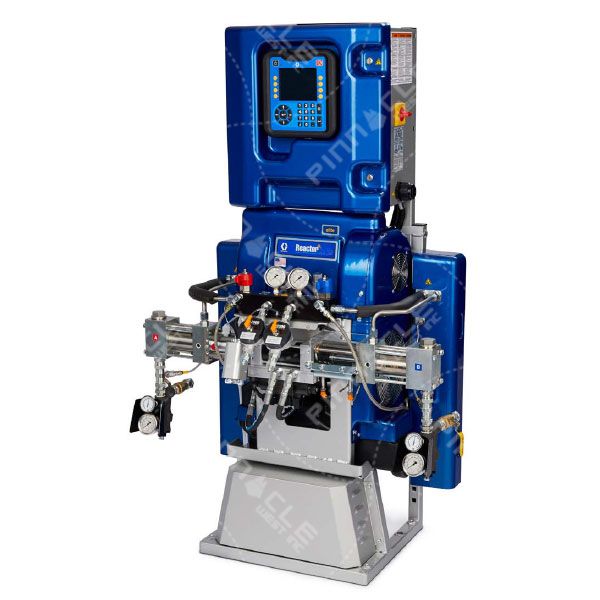 |
REACTOR 2 H-30 HYDRAULIC |
|
|
|
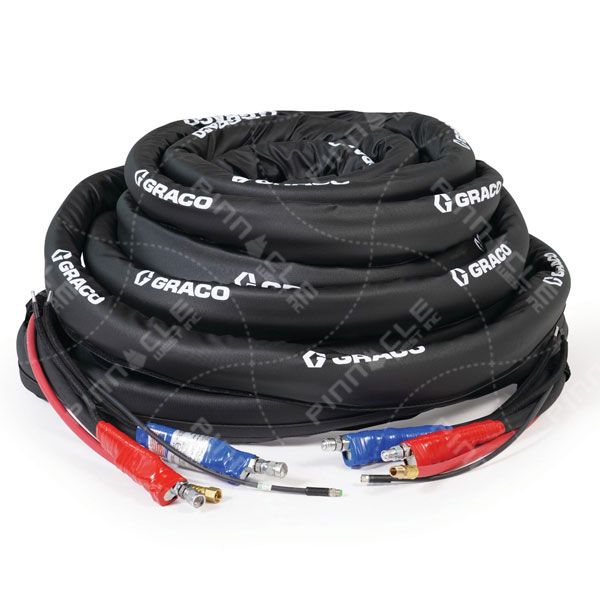 |
R2 XCELERATOR HEATED HOSE, 100 FT |
|
|
|
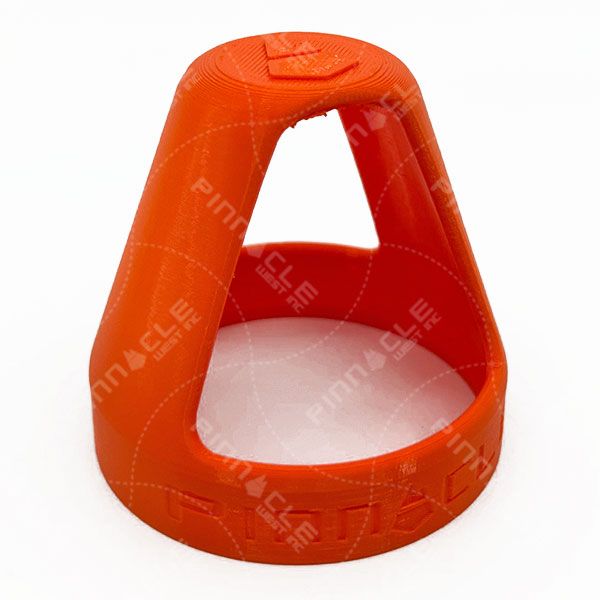 |
AEROSOL CAN NOZZLE SAVER |
|
|
|
|
|